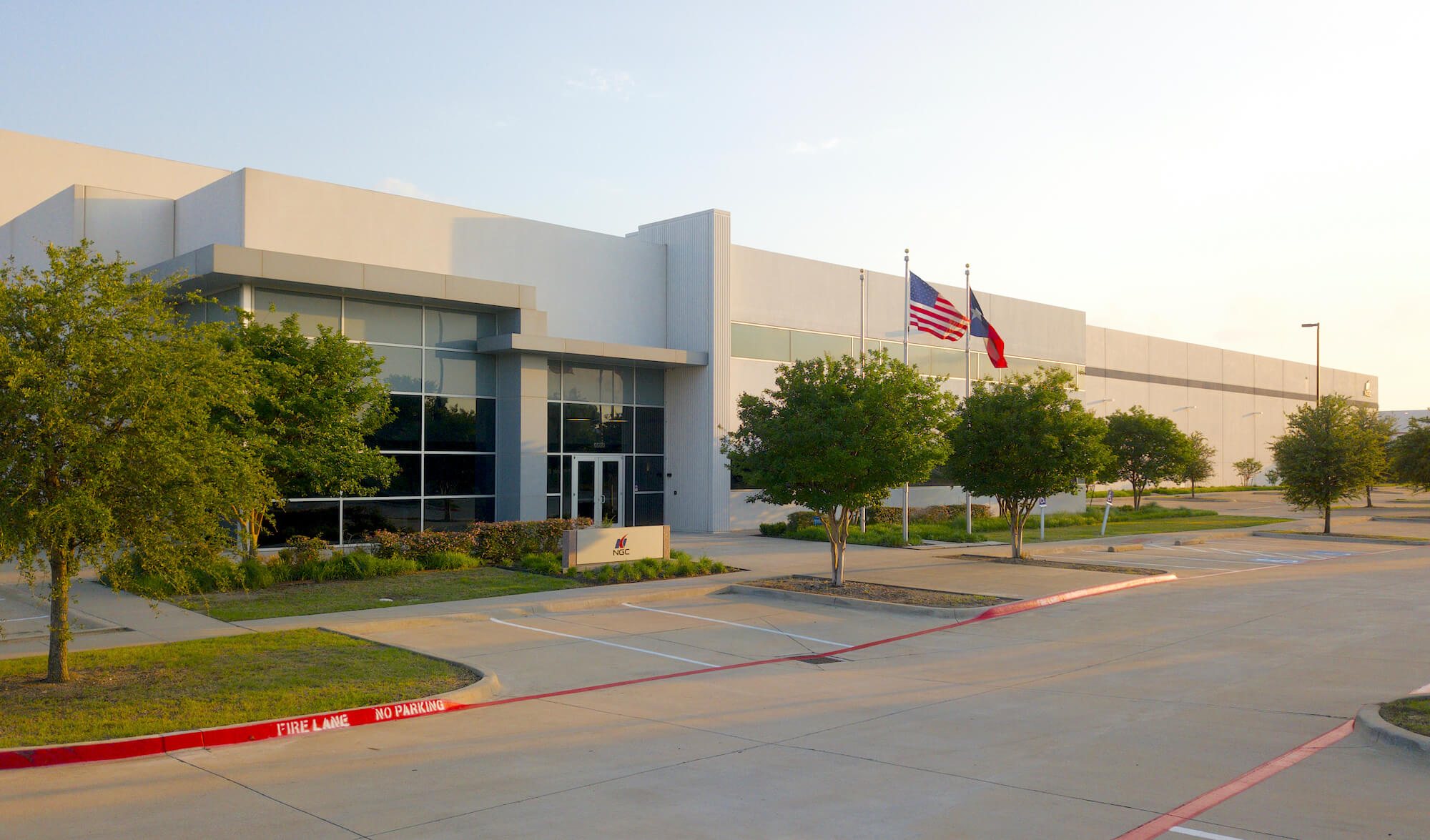
An Investment In Our People, In Service To Our Customers
Our recently-constructed Fort Worth, TX Service Center is 130,000 square feet dedicated to supporting American Wind Energy.
Here, our team of engineers, technicians, production, and technical support staff come together to ensure that our customers have the products, services, and support they need to sustain maximum availability of their turbine fleet.
This Facility Provides:
- High-Precision In-House Machining & Tooling
- Full-Load Testing via a 4MW Test Bench
- Climate-Controlled Gear Measuring & Grinding
- Non-Destructive Testing
- Root-Cause Analysis
This Facility is Home To:
- Onsite Storage & Product Inventory
- Spare Parts Inventory
- Dedicated Main Shaft Repair
- Remanufacturing & Down Tower Repair
- Core Exchange Program
- Training Operation
- Field Service Base of Operations
Facility Image Gallery
In-House Equipment Roster
-
RAPID 1600 – HÖFLER CYLINDRICAL GEAR GRINDING MACHINE
Top of the line, cylindrical gear grinding machine allowing NGC to grind any cylindrical gear of diameters. The machine is used to recondition the surface of the gear teeth through the grinding process to refurbish and re-certify a previously used gear. This process is used to offer a more cost-effective option for the customer during gearbox repair. Depending on the customer’s need, NGC can offer a re-certified gear set at a lower cost in comparison to a new gear set, thus making the gearbox overall cost at a more competitive price.
-
P 150 – KLINGELNBERG PRECISION MEASURING CENTER
The P150 Precision Measuring Center and Hofler 1600 cylindrical gear grinding machine go hand in hand during the gear re-certification process and is a must-have for gear inspection. This fully automatic CNC-controlled precision measuring center is used to inspect the gear tooth micro geometry before and after the gear grinding process.
An inspection prior to the grinding process is necessary to understand the existing condition of the gear tooth microgeometry, allowing NGC engineers to set appropriate grinding parameters to maintain the operational gear tolerances. Likewise, after the grinding process, another inspection is performed to confirm that all operational gear tolerances are met and the gear can be considered to be re-certified and ready for use in a wind turbine gearbox.
-
TEMPERATURE CONTROLLED ENVIRONMENT
Both Rapid 1600 and P150 are housed in a specially designed temperature-controlled environment, built with thermal panels and a separate air conditioning system. The purpose is to minimize dimensional variation between the gear inspection and grinding operations by maintaining a constant room temperature. Any fluctuations in temperature can allow gear alloys to thermally expand or contract, thus affecting the accuracy of the gear tooth geometry. NGC made the investment as an extra step, to promote the accuracy of the gear re-certification process.
-
AQUA CLEAN INDUSTRIAL PARTS WASHER
As a part of the gearbox and main shaft refurbishment process, it is critical to maintaining part cleanliness prior to part inspection, assembly, and painting. To accommodate this requirement, NGC uses an industrial-size Aqua Clean Stainless Steel parts washer system. After gearbox or main shaft disassembly, the components are thoroughly cleaned, rinsed, and dried using the washer system. Degreasing agents, high-pressure nozzle systems, and hot steam combination offer a level of part cleanliness that is significantly improved over traditional cleaning methods. The level of part cleanliness achieved through this system offers improved visibility for part inspection, minimizes foreign object debris contamination during assembly, and offers significant process efficiency.
-
4MW GEARBOX TEST BENCH
State of the art, custom-designed, and built test bench specifically for NGC gearbox service center. Allowing NGC to test gearboxes in a back-to-back fashion up to 4MW capacity. The main purpose is to load test and spin test the gearboxes assembled at NGC and confirm gearbox health while simulating up-tower operation. Designed as a digitally programmed and controlled dynamometer, the test bench can be programmed to execute a load and spin test profile, while operating on-board gearbox systems (ie. pump motors, heaters, etc.), regulating oil temperature, and oil flow, as well as monitoring oil cleanliness. For every gearbox test, gearbox health is further confirmed through 12 accelerometers instrumented across the test unit for vibration data collection, which is later analyzed and used to confirm proper gearbox operation. This vigorous test process benefits the customer as it confirms that the gearbox has been refurbished properly, without faults, and is ready for up-tower operation.
Choose a partner
continuously elevating the
customer experience.
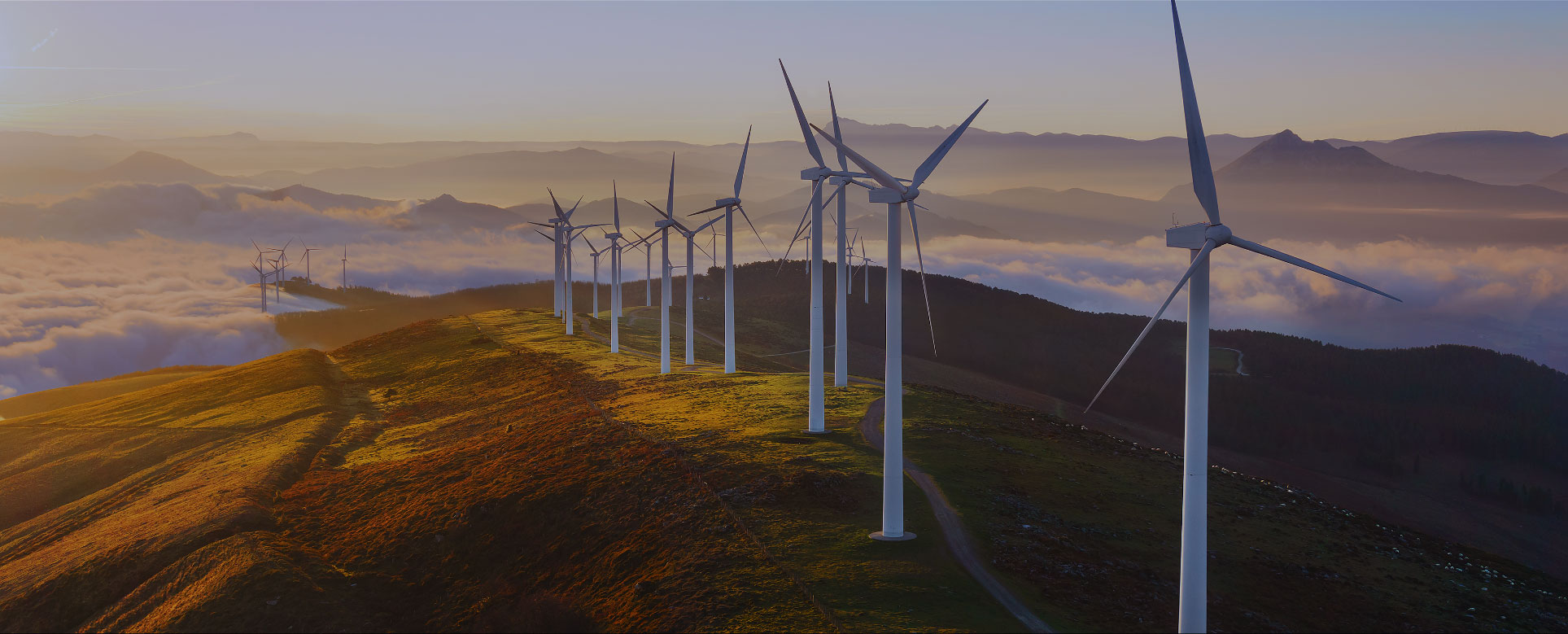